日本物質材料研究機構(NIMS)的初級研究員Jodi Dennis Edgard(九州大學研究生)、主任研究員北嶋具教(九州大學研究生院副教授)和領域負責人渡邊誠,與大阪大學研究生院工學研究科的中野貴由教授和小泉雄一郎教授組成的研究團隊,通過用照射面強度分佈均勻、光束半徑較大(平頂)的雷射照射鎳粉,成功形成了缺陷少、晶向相同的單晶。通過將其應用於雷射式3D列印機,可利用單晶製造的部件範圍將大幅擴大,不僅是飛機發動機和氣渦輪發動機的耐熱材料,還有望應用於各種單晶材料。相關内容已經發布在Additive Manufacturing Letters上。
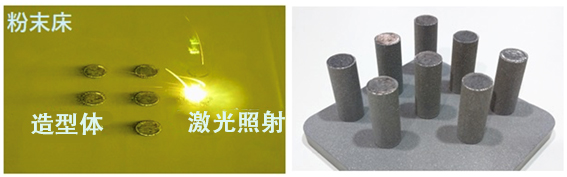
圖1:用雷射照射粉末進行造型以及造型後的造形體外觀。(供圖:日本物質材料研究機構(NIMS))
此前報告用於單晶造型的電子束方式裝置價格昂貴、需要高真空,而且運轉成本高,因此存在裝置普及率低的問題。另一方面,價格較低的雷射方式的裝置由於雷射束照射面的強度分佈遵循常態分布,因此很難在一個方向上控制固液界面的晶體成長方向,凝固時產生的巨大應變會造成晶體缺陷。所以得到的晶體是由不同取向的晶體構成的多晶體,存在有大量晶界(晶粒的界面)的問題。
研究團隊開發了利用雷射式造型裝置在不使用籽晶的情況下由金屬粉末形成單晶體的技術。此次使用了在凝固後從高溫變為低溫的過程中晶體結構不發生變化的純鎳粉末。
新技術的重點是,採用了強度分佈均勻的雷射束。雷射方式的造型裝置通過用直徑大、照射面強度分佈均勻的雷射束照射鎳粉牀,並最適化造型條件,將粉末熔化時形成的熔池形狀控制為平面狀。
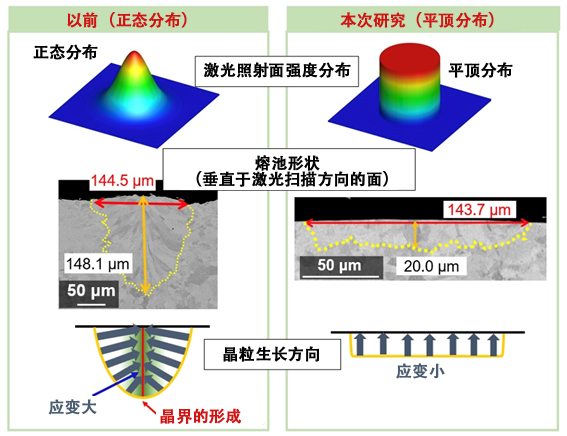
圖2:分析雷射照射的板材組織明確雷射形成的熔池形狀與組織形成的差異(供圖:日本物質材料研究機構(NIMS))
由此,將凝固時的晶體成長方向控制為與光束照射方向基本平行的一個方向。此次製作的造型體是直徑12毫米、高30毫米的圓柱體。在以前的常態分布照射面強度分佈中,固液界面會向熔池側凸起,凝固時生長的晶體在中央碰撞,形成名為晶界的面狀缺陷,同時界面附近在冷卻時會產生較大的熱收縮應變。但強度分佈均勻的雷射在凝固時,晶體會從平坦的固液界面沿光束方向生長。此時,造型過程中在前一層凝固的晶體會發揮籽晶的作用,在生長方向上具有優先取向的晶體逐漸被選擇並生長。與常態分布的雷射照射相比,凝固時的熱收縮應變會被抑制。這樣,生長晶體的取向會在一個方向上對齊,可以大幅降低凝固時晶體碰撞形成的晶界及應變造成的線狀和麪狀缺陷密度,能獲得單晶。

圖3:粉末造型體的晶體取向分佈差異(供圖:日本物質材料研究機構(NIMS))
此次的成果還可以應用於其他金屬和合金的單晶造型。尤其是飛機發動機和氣渦輪發動機的部件形狀越來越複雜化和輕量化,積層造型耐熱材料鎳基超合金的需求逐漸增加。高溫強度比多晶體優異的單晶造型體的實用化備受期待,如果能通過成本低、普及率高的雷射方式進行造型,那麼就有望在全球範圍内加速其研究和開發。
原文:《科學新聞》
翻譯編輯:JST客觀日本編輯部
【論文資訊】
期刊:Additive Manufacturing Letters
論文:Manufacturing single crystals of pure nickel via selective laser melting with a flat-top laser beam
DOI:10.1016/j.addlet.2022.100066