早稻田大學理工學術院的竹澤晃弘副教授等人組成的研究團隊宣佈,開發出了減少金屬3D列印熱變形的方法。通過在内部最適化設計晶格構造(中空構造),成功地減少了模製物體的變形。該方法有望減少大型結構物模製過程中變大的變形。相關成果已經發布在國際科學期刊《Additive Manufacturing》11月6日號上。
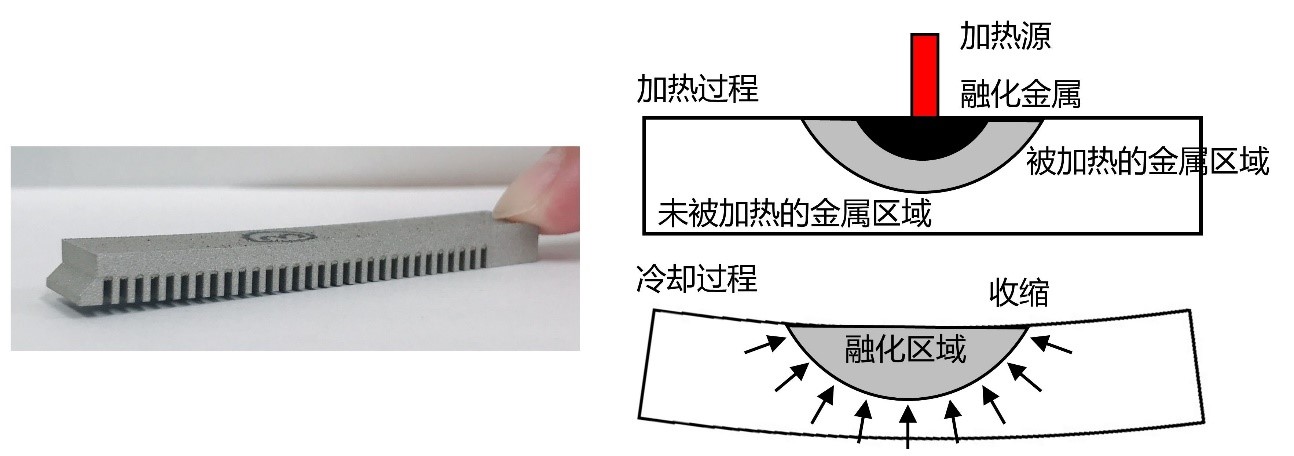
最佳晶格結構造型物(a)與截面圖(b)(供圖:早稻田大學)
近年來,金屬3D列印作為新一代加工技術得到了應用。普及最為廣泛的金屬3D列印是通過反多工雷射熔化和凝結金屬粉末薄層來形成三維結構。但在這個過程存在熔化凝結處冷卻後會產生較大的收縮應變的課題。當將造型物與底座分離時,應變會引發嚴重的翹曲,從而導致產品不合格。對此,人們一直通過在造型時預加熱來減小熔化與冷卻時的溫差,以及最適化雷射的掃描路徑等來減輕熱變形。
此次,研究團隊為了進一步減輕少變形,開發了在金屬3D列印的造型對象内部設計名為晶格的中空構造的方法。實際製作模型後確認,通過最適化配置晶格可以減少變形。一般來說,只要在模型内部設置中空構造就可以分散張力,減輕熱變形,而研究團隊分別製作了晶格均勻分布的模型和利用新方法最適化晶格分佈的模型進行了比較,發現晶格最適化分佈的模型翹曲量減少了10%以上。
開發該方法時,還利用造船型領域使用的近似計算焊接變形的簡單遞迴關係式,來表示固有應變的方法。另外,通過利用結構最適化法之一的拓撲最適化演算法,還成功開發出了旨在減輕熱變形的晶格分佈的最適化方法。
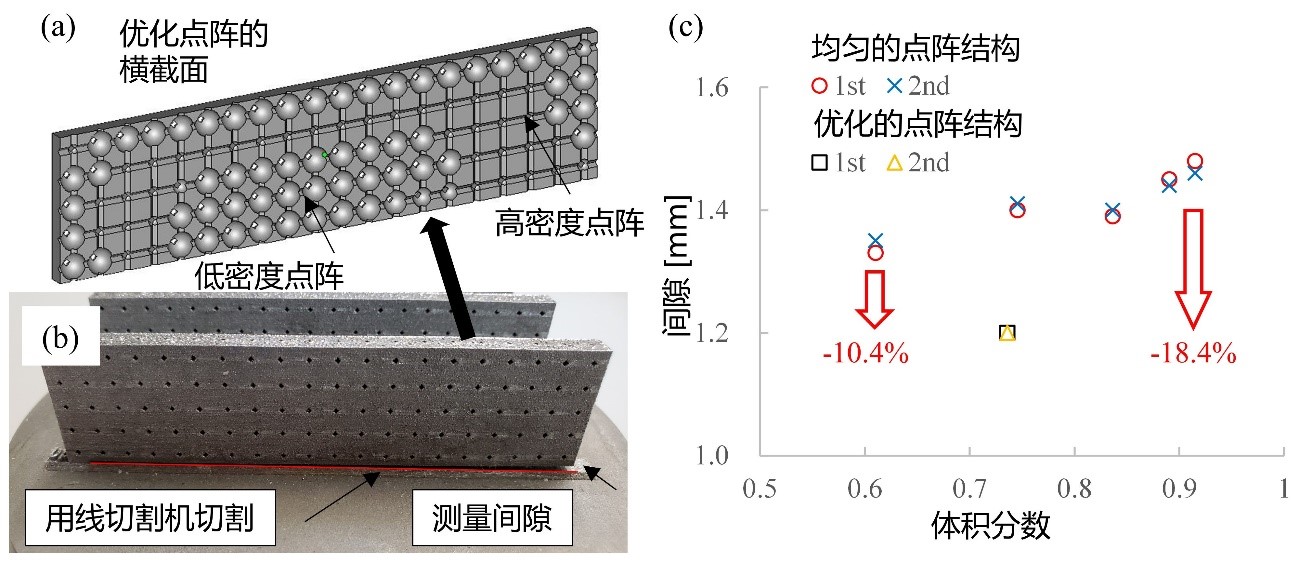
利用拓撲最適化演算法最適化晶格分佈(供圖:早稻田大學)
新開發的方法可以在模型内部形成空心球狀的晶格結構。此次雖然形成了球狀晶格結構,但形狀會因3D金屬列印機的相容性而異。模型由晶格大量分佈的低密度點陣區域和沒有晶格結構的高密度點陣區域構成。模型内部還形成了與晶格相連的格子組織狀中空結構,這是用來在形成中空結構時去除金屬粉末的。
該方法與現有的減少熱變形方法相結合的話,還可以實現更優異減少的熱變形的效果。
竹澤副教授表示:「目前正研究最適化現有的雷射掃描路徑。結合使用此次開發的技術,相信可以進一步改善熱變形問題。」
原文:《科學新聞》
翻譯編輯:JST客觀日本編輯部